Introduction
The Romeo mini robot controller is the ESP32 version of the Romeo BLE mini. It features an onboard ESP32-C3 module, supporting Wi-Fi and Bluetooth 5 dual-mode communication, and has two channels of 1.7A motor drivers.
Romeo mini has 9 IO interfaces (supporting analog, digital, UART, and I2C), with each interface compatible with the Gravity standard. It can be connected to various Gravity sensor modules. The servo interface can provide stable power supply through the servo power port for servos and other high-current devices. Additionally, it has a built-in GDI interface on the back for connecting an IPS display screen to show project-related information. The controller can meet the control requirements for robot motors and servos.
Features
- Main control + WiFi + Bluetooth 5 integrated motor driver development board
- Compact size
- Support for IPS TFT display screen
- Offers options for servo and motor control schemes
Specification
Basic Parameters:
- Main control chip: ESP32-C3-MINI-1
- Type-C input voltage: 5V
- VIN input voltage: 5-12V
- Motor output current: 1.7A continuous drive current per channel
- Servo input voltage: 5-12V
- Module size: 47x38.5mm
Interface Pins:
- Digital I/O: x4
- Analog I/O: x3
- UART: x1
- I2C: x1
- Motor: x2
- GDI: x1
- Type-C: x1
Board Overview
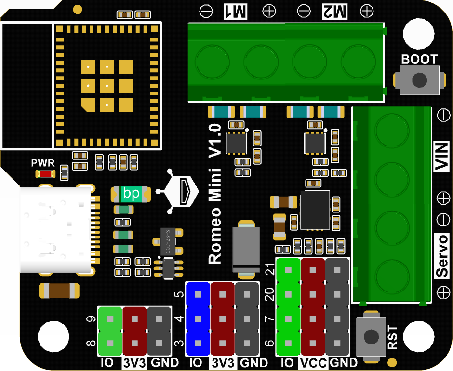
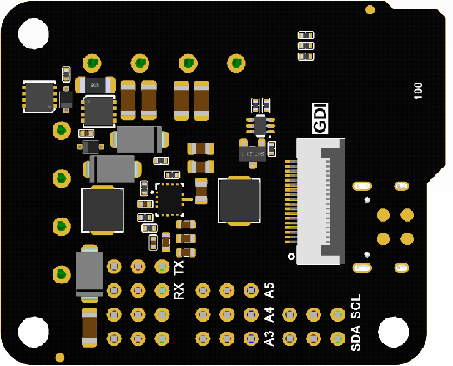
Name | Function Description |
---|---|
VIN | Power input for motor driver and controller: 5-12V. This port must be connected for M1/M2 motors to work. |
Servo | Power input for digital ports: 5-12V. If using high-current peripherals with voltage higher than 5V on digital output port (VCC end), connect to this interface to avoid damaging the Type-C USB port. |
M1/M2 Ports | Two motor control ports: |
M1: GPIO1 (direction control), GPIO0 (PWM control) | |
M2: GPIO10 (direction control), GPIO2 (PWM control) | |
I2C | Standard I2C interface: SDA (8), SCL (9), VCC (3.3V), GND |
A-3.3V-GND | Standard analog interface: |
A (blue): analog ports 3, 4, 5 | |
3.3V (red): power supply positive terminal | |
GND (black): power supply negative terminal | |
D-VCC-GND | Standard digital interface: |
D (green): digital ports 6, 7, 20, 21 | |
VCC (red): power supply positive terminal (When the Servo port is not powered, VCC is 5V; when the Servo port is powered, VCC is the input power for the Servo port.) | |
GND (black): power supply negative terminal | |
UART | RX (20), TX (21), VCC (5V), GND |
Note: The UART interface shares two IO ports with servo ports, so UART cannot be used when servos are used. | |
RST | Controller reset button |
BOOT | Controller download button |
Dimension Drawing
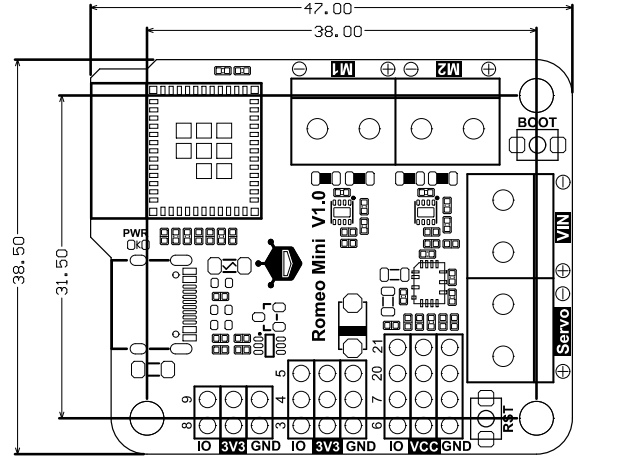
Tutorial
1. Arduino Environment Configuration
When using the ESP32-C3 development board for the first time, it is important to follow these steps:
Note: If your computer fails to recognize the Romeo Mini module when connected via USB, please press and hold the BOOT button, then press the RST button. Finally, release both the BOOT and RST buttons simultaneously.
1.Add the JSON link to the IDE.
2.Download the core of the main controller.
3.Select the development board and serial port.
4.Open the sample program and upload it.
5.Familiarize yourself with the Serial Monitor.
-
Arduino IDE Compilation Environment Configuration
-
Configure the URL in the Arduino IDE.
-
Open the Arduino IDE and click File -> Preferences, as shown in the figure below:
- In the new window, click the button indicated by the red circle in the figure below:
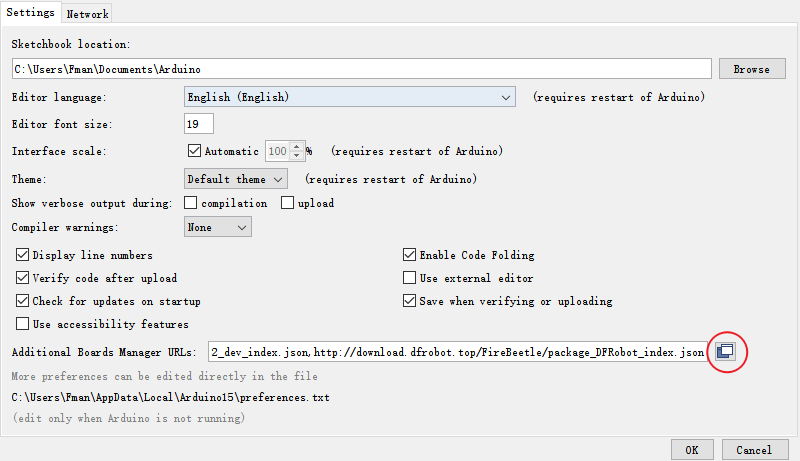
-
Copy the following link address into the dialog box that appears: https://raw.githubusercontent.com/espressif/arduino-esp32/gh-pages/package_esp32_index.json
-
Note: If you have previously installed other environments, you can press Enter at the beginning or end of the previous link and paste the above link on any line above or below it.
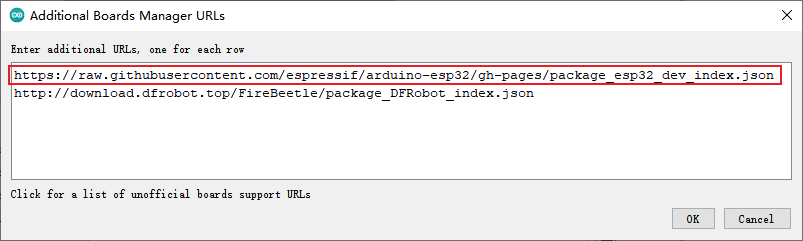
- Click OK.
- Update the board.
- Open Tools -> Board -> Boards Manager..., as shown in the figure below:
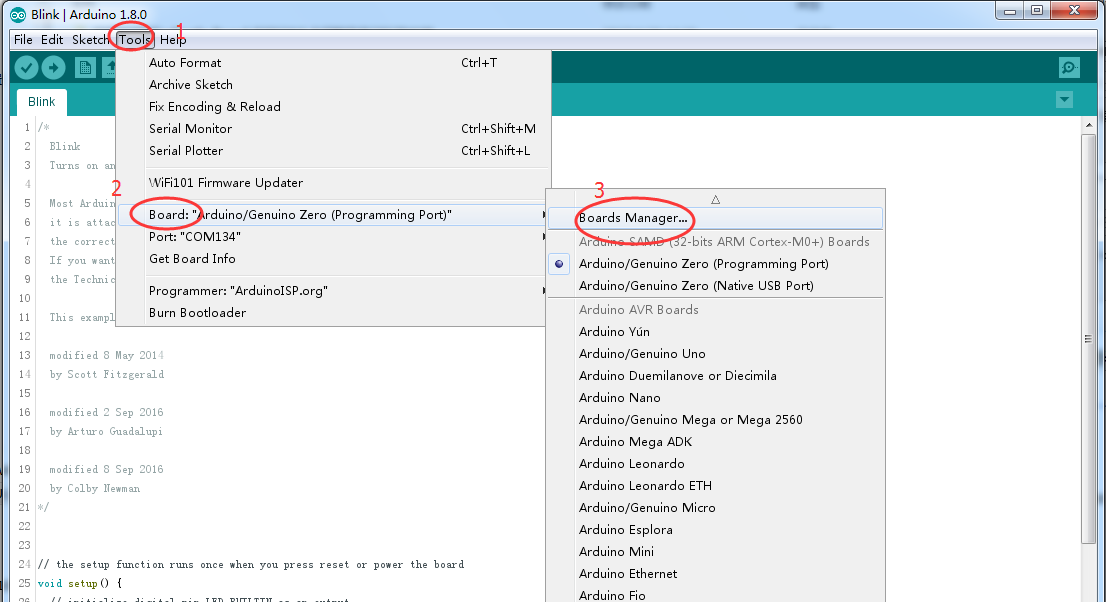
- Boards Manager will automatically update the board, as shown in the figure below:
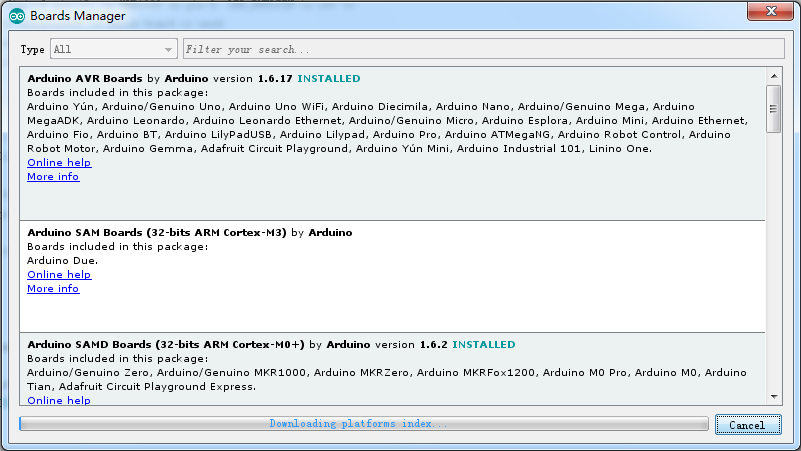
- After the update is completed, you can type "esp32" in the input box at the top. Then, select "esp32" when it appears and click Install (current version: 2.0.0):
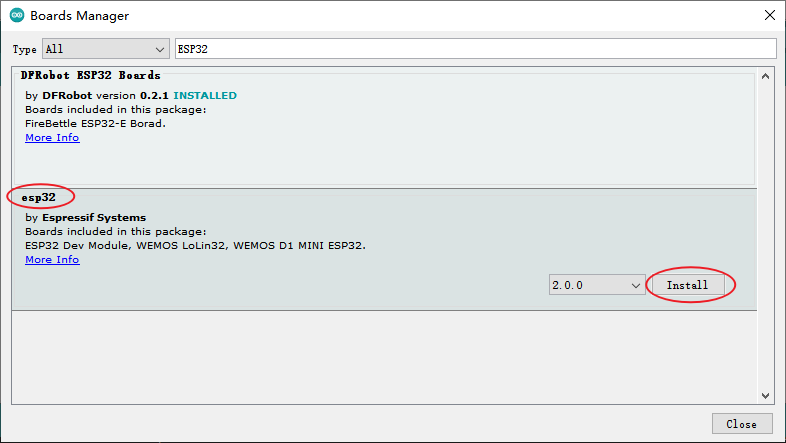
- Wait for the progress bar to finish:
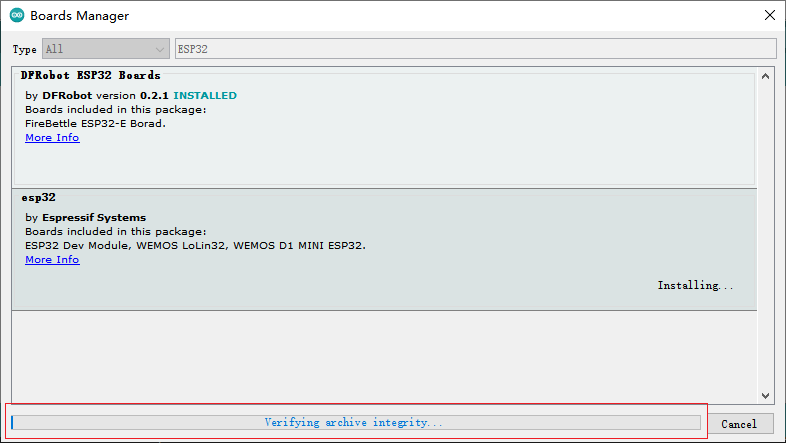
- After the installation is complete, the list will display the installed ESP32 board, as shown in the figure below:
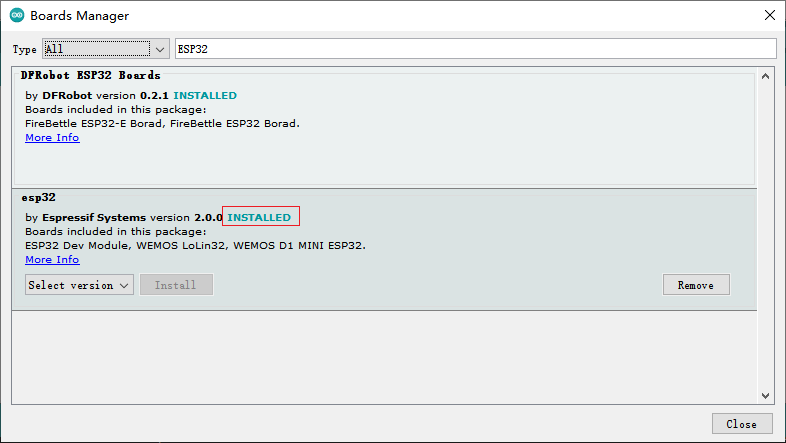
- Click Tools -> Board:, and select "ESP32C3 Dev Module" (usually the first one in the list).
- Prior to getting started, you'll need to configure the following settings (if you wish to print to the Arduino monitor via USB, choose "Enable"):
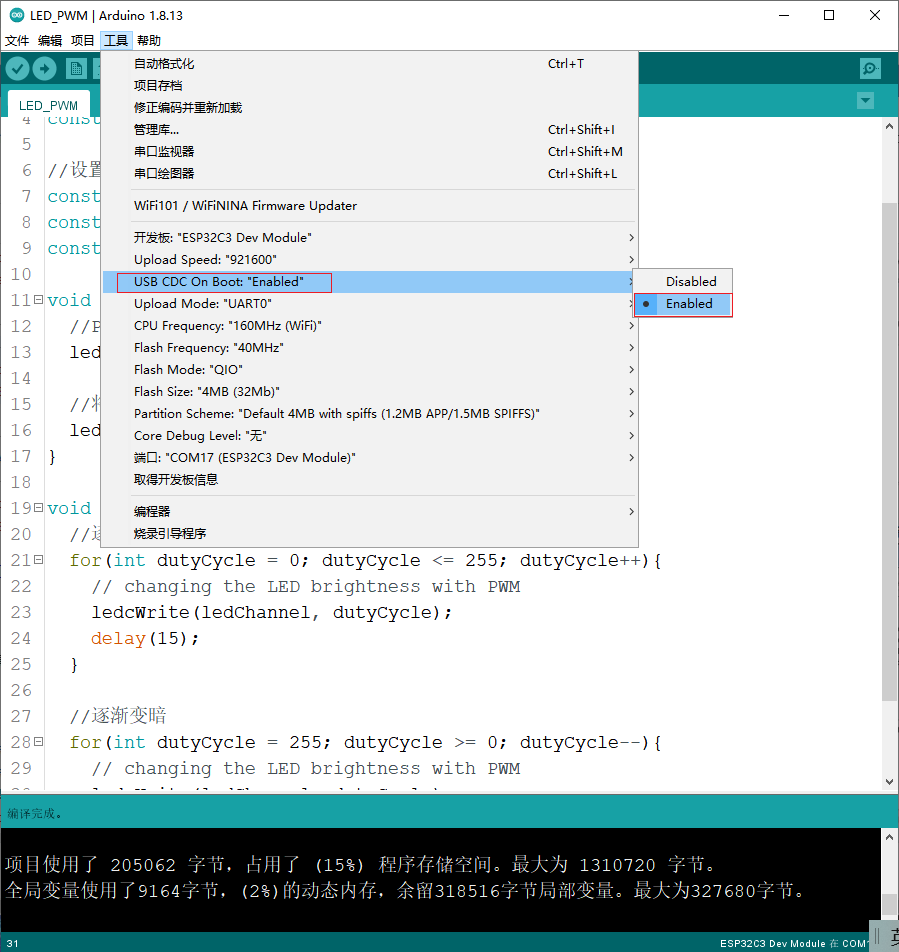
- Click on "Port" and select the corresponding serial port. (If the port keeps appearing and disappearing, you need to press and hold the BOOT button, then press the RST button, and finally release both the BOOT and RST buttons simultaneously).
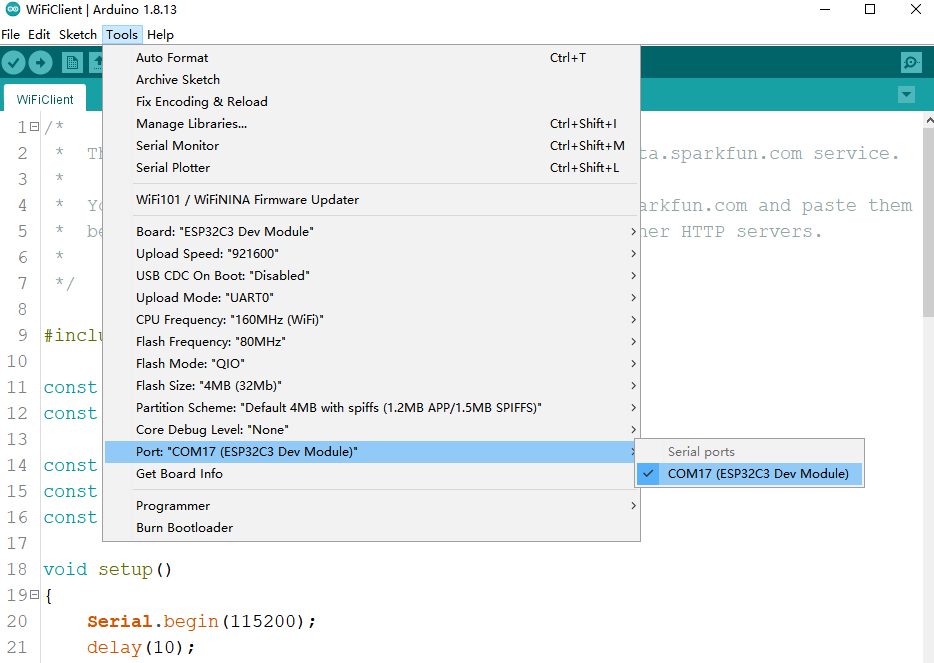
2. PWM-driven DC Motors
Requirements
-
DC Motors: x2
-
Romeo Mini: x1
Connection Diagram
The module is powered by 5-12V. Choose an appropriate power supply voltage based on the motors.
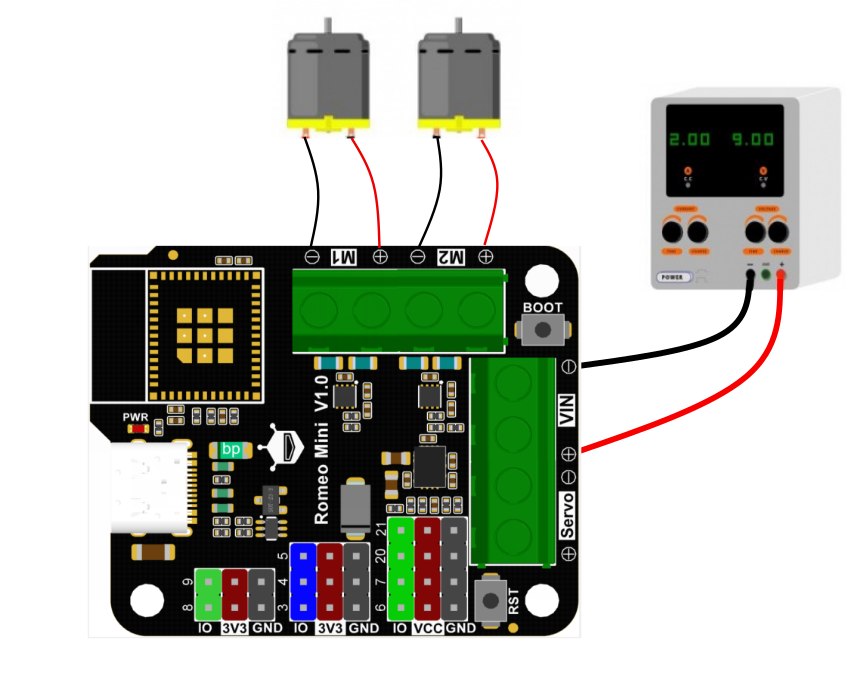
Control Modes
EN | PH | Function |
---|---|---|
H | H | Forward |
H | L | Reverse |
PWM | L | Forward |
PWM | H | Reverse |
Sample Code
int EN1 = 0; // PWM control for motor M1
int PH1 = 1; // Direction control for motor M1
int EN2 = 2; // PWM control for motor M2
int PH2 = 10; // Direction control for motor M2
void setup() {
pinMode(EN1, OUTPUT);
pinMode(PH1, OUTPUT);
pinMode(EN2, OUTPUT);
pinMode(PH2, OUTPUT);
}
void loop() {
M1_Forward(200); // Motor M1 moves forward with adjustable PWM
M2_Forward(200); // Motor M2 moves forward with adjustable PWM
delay(5000);
M1_Backward(200); // Motor M1 moves backward with adjustable PWM
M2_Backward(200); // Motor M2 moves backward with adjustable PWM
delay(5000);
}
void M1_Forward(int Speed1) // Forward fast decay mode for M1 motor, larger Speed1 value results in faster motor rotation
{
analogWrite(EN1, Speed1);
digitalWrite(PH1, LOW);
}
void M1_Backward
Example Result: Execute the sample program by commanding simultaneous rapid forward rotation of motors M1 and M2, followed by simultaneous slow reverse rotation of motors M1 and M2.
3. PWM-Driven Servo Motor
Prerequisites:
-
5V PWM servo motor x1
-
Romeo mini x1
Connection Diagram:
If you need to operate a servo motor or peripheral device with a voltage higher than 5V, connect the Servon terminal to the power supply. The power supply range should be between 5-12V. The VCC terminal voltage is equal to the input voltage at the Servon terminal. When the Servon terminal is not connected, the default VCC terminal voltage is 5V.

Sample Code
void setup() {
ledcSetup(0, 5000, 10); // Configure channel 0 with a frequency of 5KHz and 10-bit resolution
ledcAttachPin(6, 0); // Assign pin 6 as the output pin for channel 0
}
void loop() {
ledcWrite(0, 125); // Set the output of channel 0 to 125, producing a PWM output of 0 to 100% (0 to 1024)
delay(1000);
ledcWrite(0, 25);
delay(1000);
}
Example Result: Burn the sample program to cyclically rotate Servo 1 in the range of 0-180°.
4. Driving an SPI Display
Prerequisites:
-
Romeo mini x1
-
The DFR0664, DFR0649, DFR0847, DFR0928, and DFR0995 models are all compatible with the Romeo mini controller. For detailed usage instructions, please refer to the display's wiki page.
Connection Diagram:
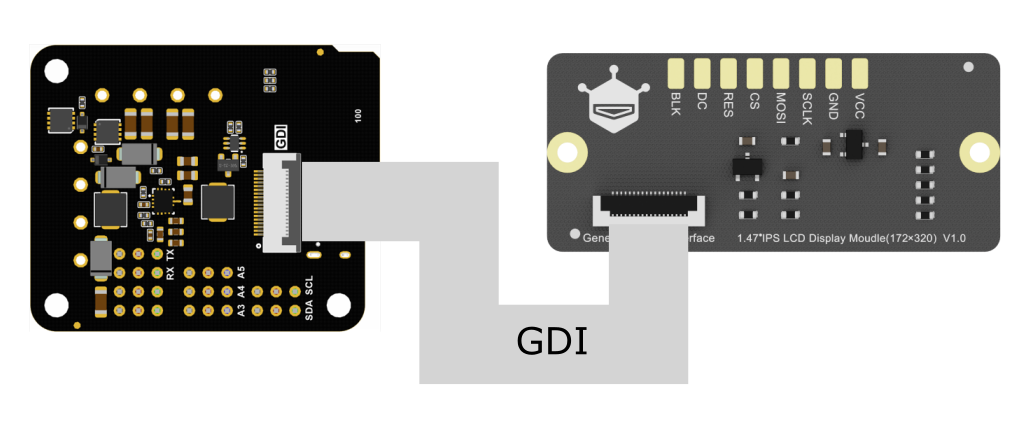
Sample Code
#include "DFRobot_GDL.h"
#define TFT_DC 8
#define TFT_CS 7
#define TFT_RST 9
DFRobot_ST7789_172x320_HW_SPI screen(/dc=/TFT_DC,/cs=/TFT_CS,/rst=/TFT_RST);
/* M0 mainboard DMA transfer */
//DFRobot_ST7789_172x320_DMA_SPI screen(/dc=/TFT_DC,/cs=/TFT_CS,/rst=/TFT_RST);
void setup() {
screen.begin();
screen.setTextSize(2);
screen.fillScreen(COLOR_RGB565_BLACK); // Set the background color
screen.setFont(&FreeMono24pt7b); // Set the font size (9, 12, 18, 24)
screen.setCursor(/x=/32, /y=/200); // Set the text position
screen.setTextColor(COLOR_RGB565_LIGHTGRAY); // Set the text color
screen.setTextWrap(true);
screen.print("DF"); // Display the English characters
}
void loop() {
// Empty loop as no further actions are required for this example
}
Example Result: Burn the sample program to display the gray English characters "DF" on the screen.
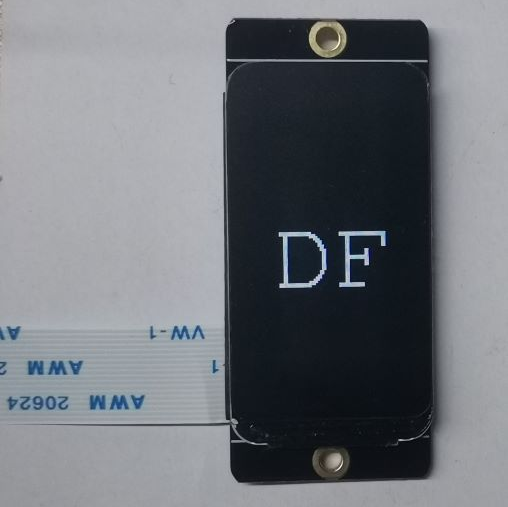
Frequently Asked Questions
Burn Error
Cause
- If the delay in the loop is too short or no delay is added, it can result in a timeout error during the burning process.
- Incorrectly calling certain functions can cause the computer to not recognize the USB connection.
Solution
Press and hold the BOOT button, then click the RST button, and finally release the BOOT button.
No Serial Output
Solution
- Check if USB CDC is enabled.
- Use a different serial debugging tool to view the print information.
- For more questions and interesting applications, you can visit the forum for reference or to post your queries.